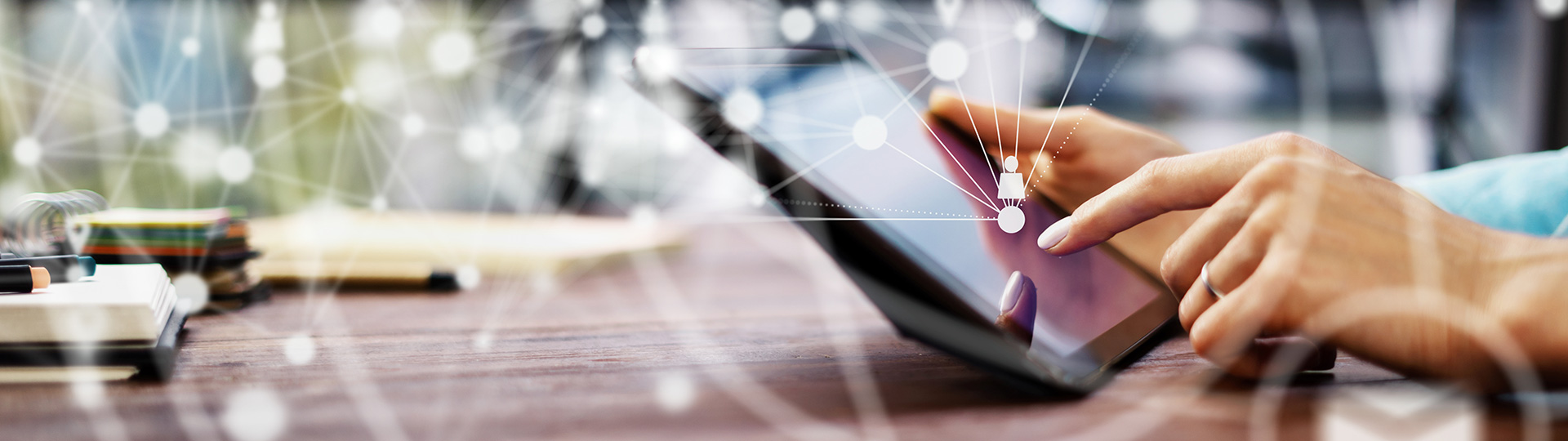
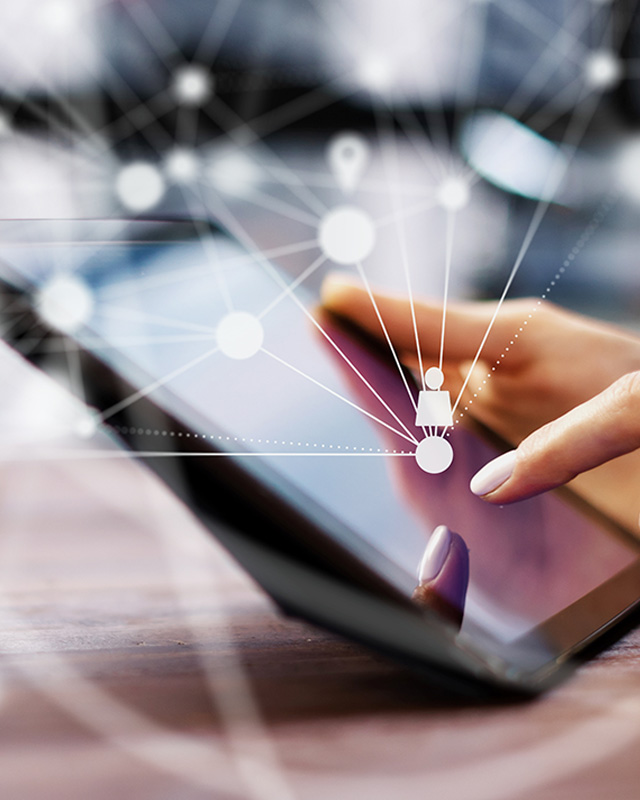
W swojej siedzibie w Bazylei, w Szwajcarii, firma F. Hoffmann-La Roche AG planuje budowę nowego budynku na potrzeby badań nad zwierzętami. Niniejsza specyfikacja opisuje autoklaw, znany również jako package unit (PU), używany do sterylizacji umieszczonych w nim przedmiotów. Autoklaw służy również do inaktywacji materiałów ABSL-2. Specyfikacje techniczne Roche obejmowały wymóg montażu siedmiu (7) PU w budynku w siedmiu strefach barierowych. Kolejny autoklaw w ósmej strefie barierowej ma być dodatkowo wyposażony w funkcję napełniania gazem. Na podstawie tej specyfikacji technicznej firma MMM Sterilisatoren AG z siedzibą w Rudolfstetten/Szwajcaria otrzymała kontrakt. Projekt rozpoczął się w 1. kwartale 2017 roku i został ukończony w 1. kwartale 2020 roku.
W projekcie budowlanym Roche „Budowa 98” osiem nowych sterylizatorów parowych do hodowli zwierząt miało mieć najwyższy możliwy stopień automatyzacji i komunikacji z istniejącą infrastrukturą IT. W tym celu sterylizatory MMM serii Vakulab HL 191221-2G oprócz zintegrowanego sterownika PLC i systemu wizualizacji (HMI) z komputerem przemysłowym Siemens zostały wyposażone w interfejs do systemu Transport Order Manager (TOM), a także w panel TOM zintegrowany ze sterylizatorem. Oprócz wielu aspektów technologicznych tego projektu, szczegółowo rozważone zostaną następujące kwestie:
Jednym z głównych wyzwań dla koncepcji automatyzacji sterylizatorów było opracowanie koncepcji bezpieczeństwa, która w zależności od wyboru umożliwia w pełni automatyczną lub ręczną obsługę, a jednocześnie spełnia najwyższe wymagania w zakresie bezpieczeństwa pracy personelu obsługi.
Krytyczną strefą niebezpieczną, którą należy zabezpieczyć, jest dostęp do komory sterylizatora przez drzwi sterowane automatycznie. Do zabezpieczenia tej strefy niebezpiecznej wybrano bezdotykowe urządzenia ochronne w postaci kurtyny świetlnej bezpieczeństwa. Jeśli nastąpi przerwanie kurtyny świetlnej bezpieczeństwa, np. gdy do komory wejdą ludzie, bezdotykowe urządzenia ochronne uruchomią stop awaryjny, aby nie dopuścić do zamknięcia drzwi komory. Aby jednak umożliwić AGV (Automated Guided Vehicle) przejazd do komory z wózkami, bezdotykowe urządzenia ochronne wyposażono w funkcję Muting.
Muting to bezpieczne, automatyczne i tymczasowe obejście bezdotykowych urządzeń ochronnych. Odpowiednia liczba i rozmieszczenie czujników funkcji muting bezpośrednio przed bezdotykowymi urządzeniami ochronnymi i za nimi zapewnia, że funkcja muting uruchamia się tylko wtedy, gdy wózki są transportowane przez AGV. Udało się to zrealizować przez jednoczesną aktywację dwóch przeciwległych czujników muting w celu uruchomienia funkcji muting.
Podczas gdy bezdotykowe urządzenie ochronne jest tymczasowo pomijane przez aktywną funkcję muting, dostęp do strefy niebezpiecznej jest całkowicie zablokowany przez wózki, co uniemożliwia ludziom dostęp do tej strefy. Gdy tylko wózek minie czujniki bezdotykowego urządzenia ochronnego i czujniki muting i nie zostaną one ponownie aktywowane, nastąpi ponowne aktywowanie kurtyny świetlnej bezpieczeństwa.
Jeśli osoba wejdzie do strefy zagrożenia, funkcja muting nie zostanie aktywowana, ponieważ odpowiednie czujniki nie zostaną aktywowane w tym samym czasie. W takim przypadku kurtyna świetlna bezpieczeństwa pozostanie aktywna, a podczas mijania jej nastąpi aktywowanie stopu awaryjnego. Za pośrednictwem modułów komunikacyjnych sterownika PLC sterylizatora stop awaryjny jest również przekazywany do systemu TOM na miejscu.
W normalnym trybie pracy sterylizatory są zintegrowane z w pełni zautomatyzowanym systemem logistycznym, sterowanym przez system TOM (Transport Order Manager) w celu załadunku i, w zależności od wyboru, rozładunku poza strefą bariery. Przełącznik wyboru trybu pracy umożliwia operatorowi indywidualne przełączanie między trybem automatycznym a ręcznym w każdym sterylizatorze. Dwukierunkowa komunikacja między sterylizatorem a systemem TOM odbywa się za pośrednictwem zmiennych w module danych sterownika PLC sterylizatora. Dostęp do modułu danych za pośrednictwem systemu TOM odbywa się przez Profinet.
a) Tryb automatyczny
W trybie automatycznym funkcje takie jak ruch drzwi, wybór programu i uruchomienie programu za pośrednictwem interfejsu HMI sterylizatora są wyłączone przez oprogramowanie. Sterylizator jest obsługiwany wyłącznie przez system TOM lub panel TOM.
Gdy pojazd AGV jest gotowy do załadunku, system TOM wysyła do sterylizatora używany program oraz polecenie otwarcia drzwi. Gdy tylko sterylizator zgłosi, że drzwi są całkowicie otwarte, rozpoczyna się załadunek przez pojazd AGV. Pojazd AGV wjeżdża załadowanym wózkiem do komory, odstawia go, a następnie ponownie wyjeżdża z komory. Podczas tego procesu system TOM wysyła do sterylizatora informację, że w komorze znajduje się pojazd AGV. Dopóki ta zapamiętana informacja nie zostanie zresetowana, sterylizator nie zaakceptuje polecenia zamknięcia drzwi. Zapobiega to przypadkowemu pozostaniu pojazdu AGV w komorze w trakcie procesu sterylizacji.
Po zakończeniu załadunku system TOM usuwa informację, że w komorze znajduje się pojazd AGV i wysyła polecenie zamknięcia drzwi. Gdy tylko sterylizator zgłosi, że drzwi są całkowicie zamknięte, system TOM wysyła polecenie uruchomienia programu. Polecenia związane z bezpieczeństwem systemu TOM są wykonywane przez sterylizator tylko wtedy, gdy pozwala na to stan pracy (np. otwieranie drzwi tylko wtedy, gdy w komorze nie ma ciśnienia).
Rozładunek w strefie bariery odbywa się zwykle ręcznie, chociaż opcja w pełni automatycznego rozładunku przez pojazd AGV również jest dostępna poza strefą bariery.
Sterylizatory zapewniają liczne zmienne statusu, takie jak przewidywany pozostały czas programu. Umożliwia to optymalne planowanie i sterowanie przebiegiem pracy przez system TOM.
b) Tryb ręczny
Aby wykonać programy testowe lub programy walidacji procesu, polecenia takie jak ruch drzwi, wybór programu i uruchomienie programu operator może wykonywać za pośrednictwem interfejsu HMI sterylizatora. Polecenia z systemu TOM są ignorowane w trybie ręcznym.
Osiem sterylizatorów jest podłączonych do systemu zasilania parą dostępnego na miejscu. Ilość pary wymagana przez sterylizatory nie może przekraczać ilości dostępnej pary. Wprowadzony przez MMM system zarządzania parą z oddzielnym sterownikiem PLC zapewnia, że nie zostanie przekroczona maksymalna liczba sterylizatorów, które w tym samym czasie znalazły się w fazie o wysokim zużyciu pary. Liczbę sterylizatorów można dowolnie konfigurować w zależności od ilości dostępnej pary.
System zarządzania parą jest zbudowany ze sterownika PLC Siemens oraz interfejsu HMI Siemens do systemu wizualizacji. Połączenie ze sterylizatorami odbywa się za pośrednictwem protokołu TCP/IP z Open User Communication (OUC). System zarządzania parą cyklicznie wysyła pakiet danych kolejno do wszystkich włączonych sterylizatorów i analizuje pakiety danych odpowiedzi. Mechanizm ten służy do zarządzania uwalnianiem pary do sterylizatorów. Gdy tylko zgłosi się maksymalna liczba sterylizatorów do zużycia pary, pozostałe sterylizatory nie będą mogły uruchomić programu.
W sterylizatorach MMM parametry sekwencji programowych maksymalnie 50 programów można w większości regulować na podstawie wartości nastawczych. Oprócz standardowych możliwości ustawień, takich jak temperatura i czas sterylizacji, np. rejestrowane wartości czujników, gradienty ciśnienia i przebieg fazy wstępnej, można konfigurować za pomocą parametrów. Aby spełnić wymóg zestrajania parametrów między ośmioma sterylizatorami, wprowadzono możliwość synchronizacji parametrów. Przez naciśnięcie przycisku można wyeksportować parametry jednego sterylizatora i zaimportować do innego sterylizatora. Podczas eksportu parametry są kopiowane do katalogu na zewnętrznym serwerze za pomocą skryptu WinCC Runtime Advanced. Podczas importu skrypt kopiuje parametry z zewnętrznego serwera do sterylizatora.
System działa bez konieczności stosowania skomplikowanego i drogiego sprzętu ani oprogramowania SCADA. Ten sam mechanizm można również wykorzystać do wygodnego tworzenia kopii zapasowych i przywracania parametrów. Dzięki zaimplementowanemu mechanizmowi synchronizacji parametrów można ponadto np. przenieść parametry określone podczas walidacji procesu w jednym sterylizatorze do wszystkich pozostałych siedmiu sterylizatorów po zatwierdzeniu. Zapewnia to dostępność identycznych zestawów parametrów we wszystkich sterylizatorach.
W hodowli zwierząt napełnianie nadtlenkiem wodoru stosuje się często jako metodę redukcji zarazków przy włączaniu i wyłączaniu przedmiotów wrażliwych na temperaturę do strefy bariery. Oprócz różnych typów śluz do napełniania gazem można również używać sterylizatorów o dużej pojemności z odpowiednim wyposażeniem technicznym. W tym przypadku sterylizatory są połączone na przykład z generatorem nadtlenku wodoru, a sterylizator działa jak śluza dekontaminacyjna. Oprócz przewodów połączeniowych do doprowadzania nadtlenku wodoru w formie jest również wymagany odpowiedni interfejs komunikacyjny między sterylizatorem a generatorem H2O2, aby zapewnić bezpieczną pracę. W niniejszym projekcie generator H2O2 miał być używany w zależności od wyboru zarówno do napełniania gazem istniejącej śluzy, jak i sterylizatora. Jako połączenie między sterylizatorem a generatorem H2O2 zastosowano odpowiedni interfejs komunikacyjny za pośrednictwem bloków danych. Cykl redukcji zarazków można rozpocząć bezpośrednio na sterylizatorze. Sterylizator stwarza podstawy dla procesu H2O2 i otwiera zawory na przyjęcie H2O2. Interfejs komunikacyjny jest następnie używany do aktywowania cyklu napełniania gazem ze sterylizatora do generatora H2O2. Sterowanie procesem cyklu redukcji zarazków jest regulowane przez generator H2O2 za pomocą następujących elementów:
Podczas gazowania komora jest odcięta od reszty systemu przewodów rurowych za pomocą zaworów. Po zakończeniu gazowania przewód zasilający i przewód ssący zamykają odpowiednie zawory. Proces napełniania H2O2 w generatorze jest zakończony. Następnie następuje regeneracja w sterylizatorze przez kilkakrotne opróżnienie komory. Po każdym opróżnieniu następuje pomiar stężenia H2O2 w komorze pod ciśnieniem otoczenia za pomocą czujnika H2O2 LC. Stężenie H2O2 musi wynosić ≤ 0,5 ppm, aby przejść do kolejnego etapu cyklu, w przeciwnym razie ponownie nastąpi etap usuwania gazu z pomiarem H2O2. Następnie komora jest napowietrzana do ciśnienia atmosferycznego. Dla większego bezpieczeństwa operatora czujnik H2O2 LC mierzy również stężenie H2O2 w komorze agregatu sterylizatora w fazach, w których nie jest aktywny żaden program, monitorując w ten sposób utrzymanie maksymalnie dopuszczalnego stężeniem H2O2 na stanowisku pracy. Projekt 13.01. Autoklaw pomyślnie przekazano do użytku w Roche w roku 2020.
Autorzy: dr inż. Martin Bönisch, inż. (FH) Axel Ehrich, MMM Group Planegg/Monachium (D)
Zdjęcia: Beat Ernst; © F. Hoffmann-La Roche AG + MMM Group, Planegg/Monachium, Niemcy)
MMM Group
Semmelweisstraße 6
82152 Planegg/Monachium
Niemcy
Obsługa klienta