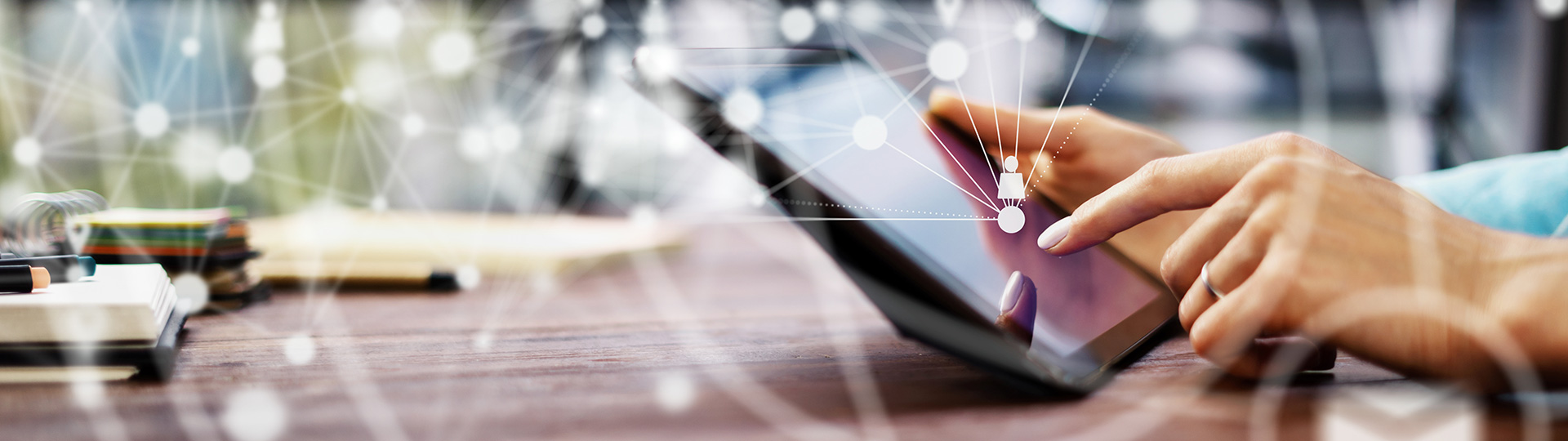
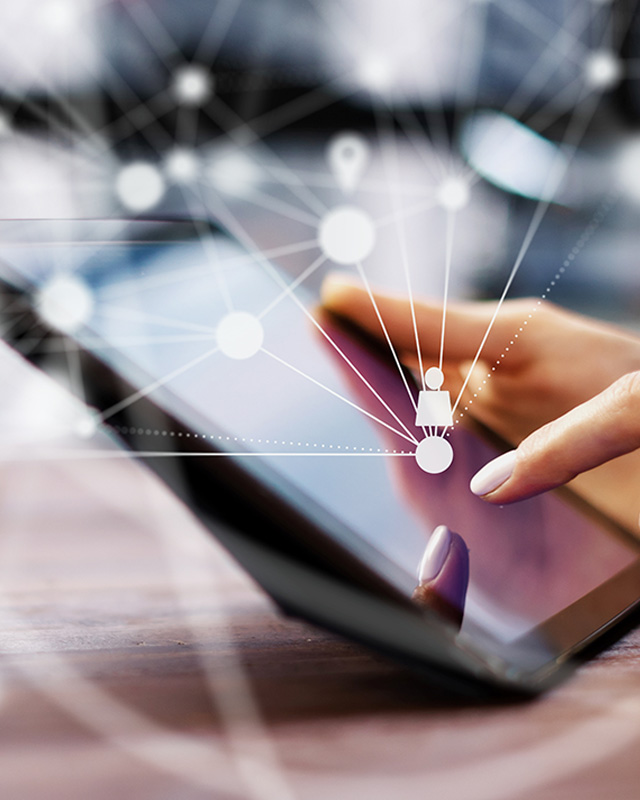
The company F. Hoffmann-La Roche AG is planning a new building for animal research purposes at its Swiss location, Basel. The specification provided describes an autoclave, also referred to as a Package Unit (PU), that is to be used for sterilizing introduced items. The autoclave will also be used to inactivate ABSL-2 materials. The technical specifications from Roche included the requirement that seven (7) PUs be installed in seven barrier zones within the building. A further autoclave in the eight barrier zone is to be additionally equipped with a gassing function. MMM Sterilisatoren AG, which has its headquarters in Rudolfstetten/Switzerland, was awarded the contract on the basis of this technical specification. The project was started in the first quarter of 2017, and was completed in the first quarter of 2020.
In the Roche “Bau 98” construction project, the objective was to achieve the highest level of automation and connectivity to the existing IT infrastructure for the eight new steam sterilizers used for the keeping of animals. For this purpose, the MMM sterilizers in the Vakulab HL 191221-2G series, which come with an integrated PLC and visualization software (HMI) via a Siemens industrial PC, were also equipped with an interface to the on-site Transport Order Manager (TOM) as well as a TOM panel integrated into the sterilizer. Beside the many special technological requirements in this project, the following aspects also needed to be considered in detail:
One of the essential requirements on the automation concept for the sterilizers was to develop a safety concept that allows both a fully automatic and manual mode while at the same time meeting the most stringent requirements on occupational safety for the operators.
The critical hazardous area to be protected is the access to the sterilizer chamber via the automatically controlled doors. An electro-sensitive protective device (ESPD) in the form of a safety light curtain was selected to protect this hazardous area. When the safety light curtain is interrupted, e.g., when persons enter the chamber, the ESPD triggers an emergency stop to prevent the chamber door from being closed. To nevertheless allow the passage of AGVs (Automated Guided Vehicles) with trolleys into the chamber, the ESPD is equipped with a muting function.
Muting refers to the safe, automatic, and temporary bypassing of the ESPD. By positioning a suitable number of muting sensors in front of and behind the ESPD, it is ensured that the muting function is only triggered by the transport of trolleys in or out of the sterilizer by means of AGVs. This was achieved by requiring that two opposing muting sensors be activated concurrently in order to trigger the muting function.
While the ESPD is temporarily bypassed as a result of the active muting function, access to the hazardous area is completely blocked due to the trolleys and this prevents access to the hazardous area by persons. As soon as the trolley has passed the ESPD and muting sensors and the latter are no longer activated, the safety light curtain is reactivated.
When a person enters the hazardous area, the muting function is not triggered because the relevant sensors are not activated concurrently. In this case the safety light curtain remains active and an emergency stop is triggered as the person passes. The emergency stop is also reported to the on-site TOM via the communication components of the PLC.
In normal mode, the sterilizers are integrated into a fully automated logistics system for loading, and optionally unloading outside the barrier zone, that is controlled by TOM (Transport Order Manager). An operator can switch each sterilizer between automatic mode and manual mode by means of an operating mode selection switch. The bi-directional communication between a sterilizer and TOM occurs via variables in a data block in the PLC of the sterilizer. TOM accesses the data block via Profinet.
a) Automatic mode
In automatic mode, functions performed via the HMI of the sterilizer, such as door movement, program selection, and program start, are blocked by the software. The sterilizer is operated exclusively via TOM or the TOM panel.
When an AGV is ready to be loaded, TOM sends to the sterilizer the program to be used as well the command to open the door. As soon as the sterilizer reports that the door is completely open, loading by the AGV begins. The AGV transports the loaded trolley into the chamber, sets it down, and then moves back out of the chamber. During this process, TOM sends to the sterilizer the information that there is an AGV in the chamber. As long as this non-volatilely saved information is not reset, the sterilizer will not accept the command to close the door. This prevents the AGV from unintentionally remaining in the chamber during the sterilization process.
After loading is complete, TOM deletes the information that there is an AGV in the chamber and sends the command to close the door. As soon as the sterilizer reports that the door is completely closed, TOM sends the command to start the program. Safety-relevant commands from TOM are only executed by the sterilizer if allowed by the operating state (e.g., the door is only opened if the chamber is de-pressurized).
Unloading is normally performed manually within the barrier zone, whereby the option for fully automated unloading by means of an AGV outside the barrier zone is also available.
The sterilizer provides a multitude of status variables, for example the expected time remaining for the program. This makes it possible for TOM to optimally plan and control the operating sequence.
b) Manual operation
To perform test programs or process validation programs, commands such as door movement, program selection, and program start can be issued by the operator via the HMI of the sterilizer. Commands from TOM are ignored during manual mode.
The eight sterilizers are connected to an on-site steam supply. The quantity of steam required by the sterilizers must not exceed the available quantity of steam. The steam management system implemented by MMM, which has its own PLC, ensures that the maximum number of sterilizers that are concurrently in a phase with a high steam consumption is not exceeded. The number of sterilizers is freely configurable depending on the steam quantity available.
The steam management system comprises a Siemens PLC and a Siemens HMI for visualization. It is connect to the sterilizer via TCP/IP using Open User Communication (OUC). The steam management system cyclically and sequentially sends a data packet to each of the switched on sterilizers and evaluates the response data packet. The coordination of steam release to the sterilizers occurs via this mechanism. As soon as the maximum number of sterilizers requiring the consumption of steam have registered with the steam management system, the remaining sterilizers are prevented from starting a program.
In the case of the sterilizers from MMM, the program sequences for up to 50 programs are highly parameterizable by means of settings. Besides standard setting options such as the sterilization temperature and time, it is also possible to configure the sensor values to be recorded, the pressure gradients, and the steps in the preliminary phase via parameters. To satisfy the requirement for ensuring consistent parameters across all eight sterilizers, an option to synchronize the parameters was implemented. The parameters of one sterilizer can be exported, and then imported into another sterilizer at the press of a button. During export, the parameters are copied into a folder on an external server by means of a script running under WinCC Runtime Advanced. During import, a script copies the parameters from the external server into the sterilizer.
The system functions without time consuming to plan and costly SCADA hardware and software. The same mechanism can also be used to conveniently backup and restore parameters. Using the implemented mechanism for synchronizing parameters, it is also possible, for example, to transfer the parameters determined during the process validation of one sterilizer to all other seven sterilizers after the process is released. This ensures that identical parameter sets are present on all sterilizers.
In the animal keeping field, gassing with hydrogen peroxide is frequently used as a germ reduction method when transporting temperature sensitive items in and out of the barrier zone through an air lock. Besides the various air lock types that available, it is possible to use large capacity sterilizers equipped with suitable technical features to perform the gassing. In this case, the sterilizers are combined for example with a hydrogen peroxide generator and the sterilizer acts as a decontamination lock. In addition to the connection lines for supplying the vaporized hydrogen peroxide, a suitable communication interface between the sterilizer and H2O2 generator is required to guarantee safe operation. In the present project, the H2O2 generator was to be used not only for gassing an existing air lock but optionally also a sterilizer. A suitable communication interface via data blocks was implemented for connecting the sterilizer to the H2O2 generator. The germ reduction cycle can be started directly at the sterilizer. The sterilizer creates the preconditions for the H2O2 process and enables the valves for entry of the H2O2. The enable for the gassing cycle is then given by the sterilizer to the H2O2 generator via the communication interface. The procedure for the germ reduction cycle is controlled by the H2O2 generator by means of the following elements:
The chamber is isolated by valves from the other parts of the pipe system during the gassing process. When the gassing process has completed, the feed and discharge lines are closed by the corresponding valves. The H2O2 gassing process is ended at the generator. Regeneration in the sterilizer then occurs by repeated evacuation of the chamber. After each evacuation, the H2O2 concentration in the chamber is measured at ambient pressure using a H2O2 LC sensor. The H2O2 concentration must be ≤ 0.5 ppm to continue to the next cycle step, otherwise the evacuation step with subsequent H2O2 measurement is performed again. The chamber is then ventilated to atmospheric pressure. To ensure a higher level of operator safety, the H2O2 LC sensor also measures the H2O2 concentration in the assemblies compartment of the sterilizer during phases when no program is active, thereby monitoring adherence to the maximum permissible H2O2 concentration in the workplace. The 13.01 project. Successful handover of the autoclaves in January 2020 for operation at Roche.
Authors: Dr. Ing. Martin Bönisch, Dipl.-Ing. (FH) Axel Ehrich, MMM Group Planegg/Munich (D)
Photos: Beat Ernst; © F. Hoffmann-La Roche AG + MMM Group, Planegg/Munich, Germany)
MMM Group
Semmelweisstraße 6
82152 Planegg/Munich
Germany
Costumer Service