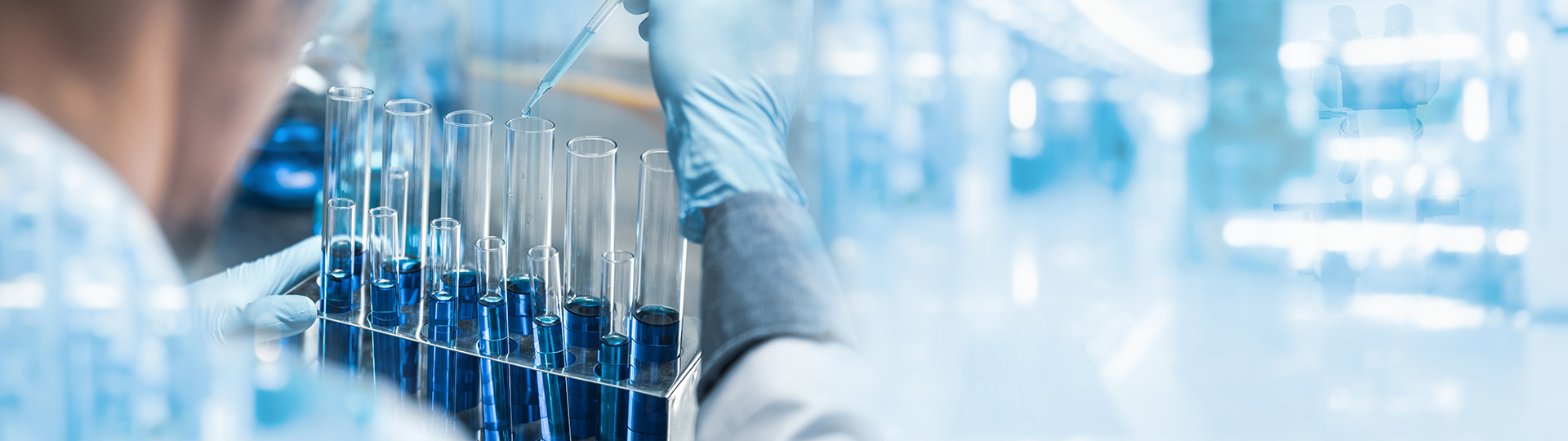
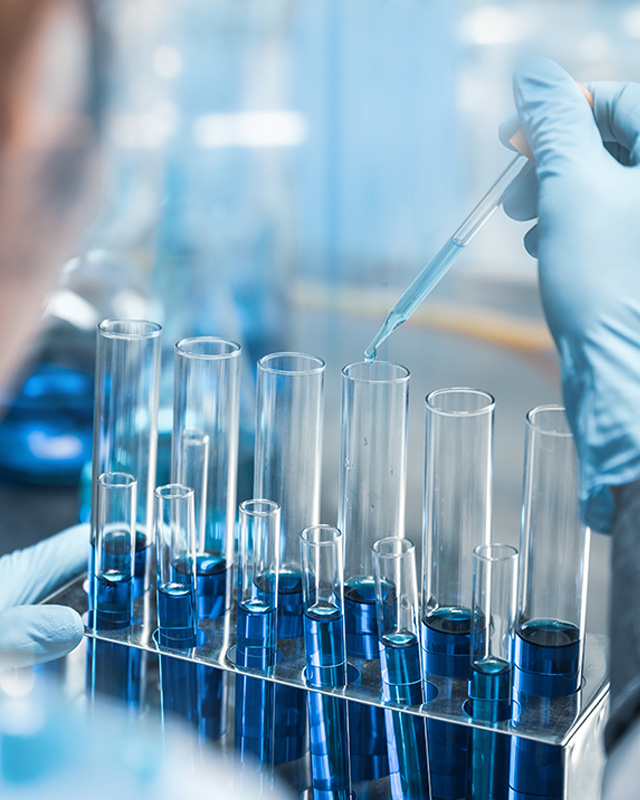
The equipment options of the Vakulab® PL H and G are so wide-ranging and versatile that they cover a particularly broad field of application. The basic configuration of both sterilizer types already satisfy all standard requirements for research laboratories, animal sciences, and industrial applications—both in terms of quality and the range of available chamber volumes.
H models (machines with horizontally opening chamber doors)
666
710 x 650 x 690
318
1.918 x 1.900 x 970
669
710 x 650 x 990
456
1.918 x 1.900 x 1.270
966
1,000 x 650 x 690
448
1,918 x 1,900 x 970
969
1,000 x 650 x 990
644
1,918 x 1,900 x 1,270
9612
1,000 x 650 x 1,350
871
1,918 x 1,900 x 1,620
G models (pit machines with horizontally opening chamber doors)
969
1,360 x 720 x 1,090
1,070
1,918 x 1,900 x 1,390
9612
1,360 x 720 x 1,390
1,360
1,918 x 1,900 x 1,690
12612
1,600 x 720 x 1,390
1,600
2,218 x 1,900 x 1,690
141114
1,550 x 1,200 x 1,500
2,770
2,150 x 3,100 x 2,070
181015
2,010 x 1,100 x 1,640
3,625
2,550 x 3,100 x 2,210
181215
2,010 x 1,300 x 1,640
4,285
2,550 x 3,500 x 2,210
Technical data subject to change without notice
The Vakulab® PL H and G is ideally suited for sterilizing solid and porous materials, liquids in open or loosely sealed containers as well as for sterilizing infectious waste and liquids in closed containers using the steam/air mixture process.
The sterilizer complies with the Pressure Equipment Directive (PED) 2014/68/EU and the Machinery Directive 2006/42/EC. CE marking according to PED 2014/68/EU. The standards applied are: DIN 58951-2 Steam sterilizers for laboratory use, AD 2000 Design of Pressure Vessels and DIN EN 62304 Medical device software. Sterilization pressure vessel, double-walled, internal walls and steam jacket made from stainless steel, material no. of the internal walls: 1.4404 (AISI 316 L)/jacket: 1.4571 (AISI 316 Ti). Piping system: Design as per DIN EN 285, steam-conducting pipes and fittings made from stainless steel; all pipes color-coded and thermally insulated. Software validation according to DIN EN 62304, electrical equipment for measurement and control according to DIN EN 285.
High-tech – harnessed intelligently
The latest generation of PLC controllers enables intuitive operation, password-protected data management, and parameter-controlled free process programmability that allows all project-specific details to be individually accounted for.
Download the brochure and find out more about the Vakulab® PL H and G
MMM Group
Semmelweisstraße 6
82152 Planegg/Munich
Germany
Costumer Service