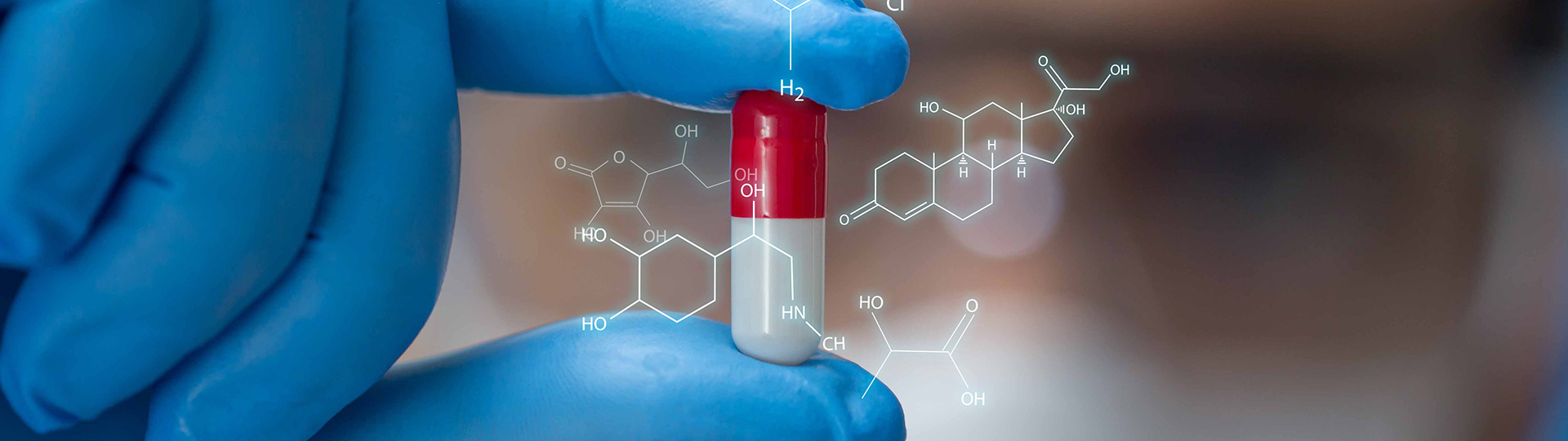
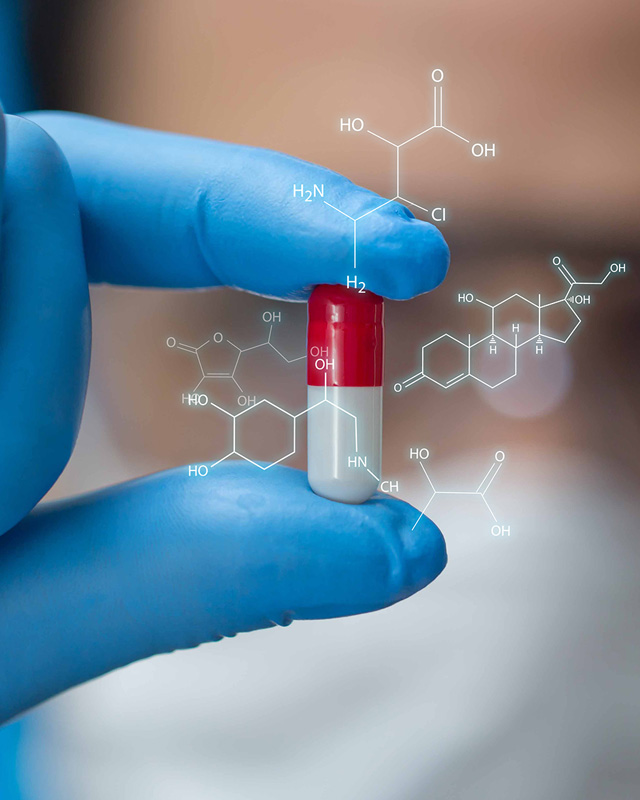
The hygienic design and customer-specific special features of the Vakulab® HL handle the demanding tasks involved in the production of sterile materials, such as solutions or filled syringes, as well as those encountered in production-related areas where the sterilization of fermenters, machine parts, clean room garments, filters, etc. calls for individual solutions.
H model 669
710 x 650 x 990
460
1.918 x 1.900 x 1.360
H model 969
1,000 x 650 x 990
644
1,918 x 1,900 x 1,360
Technical data subject to change without notice
Suitable for sterilizing solid and porous materials using the pre-vacuum process or pulsed vacuum process following by drying. Liquids in open or loosely sealed containers using the pre-vacuum process.
Liquids in tightly sealed containers made from glass or heat-resistant material using the steam/air mixture method (SAMM) (only with the steam/air mixture process option). Infectious materials (only with the Exhaust air filter feature). The sterilizer complies with the Pressure Equipment Directive (PED) 2014/68/EU and the Machinery Directive 2006/42/EC. CE marking according to PED 2014/68/EU. The standards applied are: DIN 58950, AD 2000 Design of Pressure Vessels and DIN EN 62304 Medical device software.
High-tech – harnessed intelligently
Combined with MMM’s SiSoft control software, the latest generation of Simatic controllers enables intuitive operation, password-protected data management, and parameter-controlled free process programmability that allows all project-specific details to be individually accounted for.
Precise process control
» State-of-the-art industrial controller
» Redundant sensors for superior process reliability
» PPV system: Process Parameter Verification
» Interfaces for optimal integration
The software
» Secure and user-friendly
» Software development and validation according to DIN EN 62304 Software life-cycle processes.
» The sophisticated parameter structure provides a high level of flexibility when configuring the machine
» User management features ensure excellent access security.
Custom machine configuration
» Continuous monitoring of all measured values
» Precise regulation of the actuators
» Barcode reading system with automatic program selection (optional)
» Autostart for automated program sequences, such as vacuum test, heating (optional)
» Versioning and release of programs (optional)
» Active P&ID diagram (optional)
» External communication interfaces, e.g., via Profinet (optional)
Conformity with 21 CFR Part 11
» User management
» Data archiving with checksum
» Audit trail
Download the brochure and find out more about the Vakulab® HL
MMM Group
Semmelweisstraße 6
82152 Planegg/Munich
Germany
Costumer Service